「少量生産のツール」から「量産設計ツール」への転換
大きな付加価値を生み出すADVENTUREClusterの位相最適化
従来、位相最適化は計算時間の長さや製造可能な形状の考慮が難しいことから、3Dプリンターを用いた多品種少量生産と親和性が高いとされていました。 ADVENTUREClusterでは、高速ソルバーの組み合わせと、ADVENTURECluster 2024 の新機能である型抜き制約の追加により、位相最適化の「少量生産のツール」から「量産設計ツール」へのシフトが可能となりました。
量産設計ツールへの移行がもたらす最大の利点は、スケールメリットを享受できることです。 わずかな軽量化であっても、製品のライフサイクル全体で見れば大きなコスト削減が図れます。
例えば、年間100万個製造する製品を25g軽量化できれば、年間で25トンの材料を削減することができます。 材料コストが1キログラム当たり400円とすると、年間で1000万円の材料費が浮く計算になります。 これは、日本の就業者一人当たりの付加価値額を上回る金額です。 また、CO2の排出量取引価格から換算すると、約6500トンのCO2削減に相当します。
このように、量産品においては、わずかな軽量化が国内の労働者一人分の価値やCO2削減を生み出すことができるのです。 位相最適化の進化が、製造業に新たな可能性をもたらします。
ADVENTUREClusterの位相最適化の魅力4点
1.設計工程で利用可能な高速さ
最適化計算は構造解析の繰り返しであり、計算コストが高いことが課題とされてきました。 市販の最適化ソフトでは、計算時間の長さがネックとなり、規模によっては1カ月近くかかることもあります。 計算に1カ月かかることを前提とした開発スケジュールを組むことは難しく、これでは最適化を設計プロセスに組み込むことができません。
しかし、ADVENTUREClusterの位相最適化を用いることで、この問題は解決されつつあります。 高速ソルバーの強みを生かし、1ヵ月近くかかる計算時間を3日に短縮できた例があります。 これにより、金曜日に計算をスタートし、翌週には結果を確認することができるようになります。設計工程で利用可能なレベルの計算時間が実現したことは、非常に有益です。
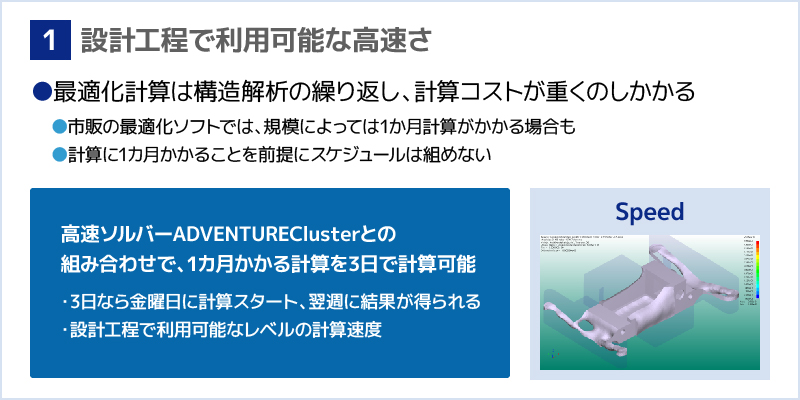
2.グレー要素の少ない明瞭な結果が得られる
疎密を計算する密度法ベースの位相最適化で問題となるのが、グレー要素です。 グレー要素とは、疎密が0.5の要素を指します。 このような中途半端な疎密は製造ができないため、構造を作るべきか、構造が不要なのかの設計判断を困難にします。グレー要素はない方が望ましいのです。
ADVENTUREClusterの位相最適化では、グレー要素の割合で計算の終了条件をコントロールすることが可能です。 こちらの結果はモデルに占めるグレー要素の割合を示しています。 許容するグレー要素の割合を指定し、明瞭な結果が得られるまで計算を継続することができます。 これにより、設計判断が容易になり、迅速な意思決定が可能となります。
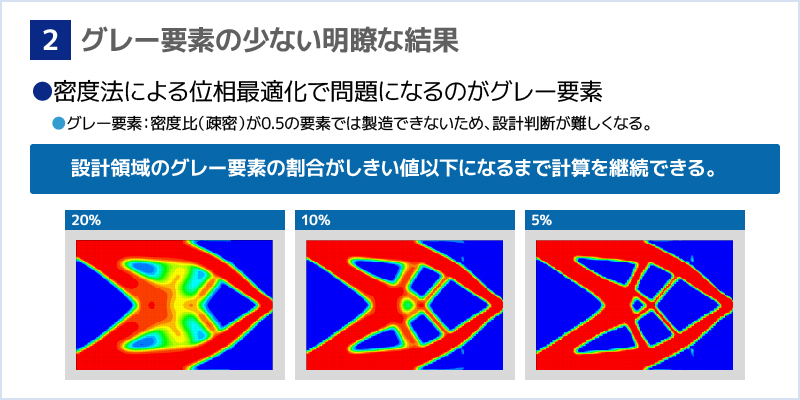
3.応力の評価が可能
応力は、切り欠きがあると応力集中が発生するように、形状に非常に敏感な物理量です。 そのため、形状を変化させる最適化においては取り扱いが難しく、市販の最適化ソフトの中には応力の評価に対応していないものもあります。 しかし、応力を評価できなければ、強度を担保した最適形状を得ることはできません。
ADVENTUREClusterの位相最適化では、Mises応力、最大主応力、最小主応力の3種類の応力を評価することが可能です。 特に、主応力の評価ができる最適化ソフトは非常に珍しく、ぜひ一度お試しいただきたいものです。 新たな発見や便利さを感じていただけることでしょう。
応力の制約条件がある場合の最適化結果を以下に示します。 左側を固定し、右側中央に荷重を与えるモデルです。
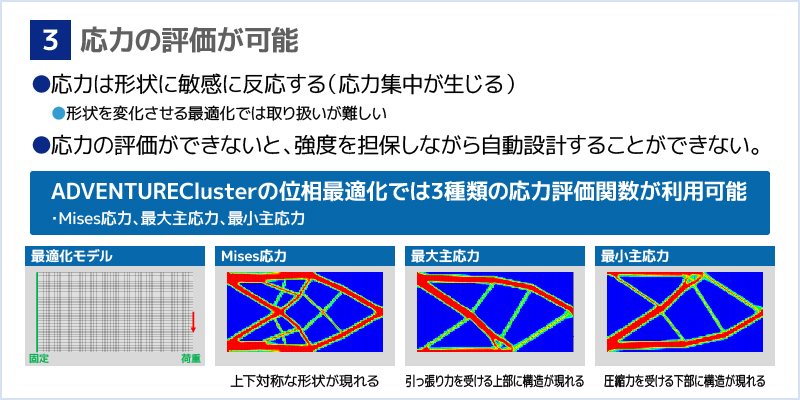
- Mises応力では上下対称な形状が現れる
- 最大主応力では引っ張り力を受ける上部に構造が現れる
- 最小主応力では圧縮力を受ける下部に構造が現れる
以上の結果となっています。 応力の評価により、強度を担保しながら自動設計を行うことができるのです。
4.型抜きの可能な形状が得られる
最後の魅力、4つ目は「型抜き可能な最適形状が得られる」ことです。 これはADVENTURECluster2024から利用可能になった注目の機能です。
最適化を設計プロセスに組み込む際、最適化結果が量産可能な形状でないと扱いづらいという課題があります。 そこで、製造条件の第一弾として、型抜き制約を実装しました。 型抜き制約は鋳造や射出成形などで型抜き可能な形状を得るための製造制約で、構造内に生じる空隙やアンダーカット形状の生成を抑制します。 これにより、金型のキャビティ側からもコア側からも離型可能な形状を得ることが可能です。
以下の最適化結果は、全体がZ方向と後部がX方向に型抜き制約がある場合の結果です。
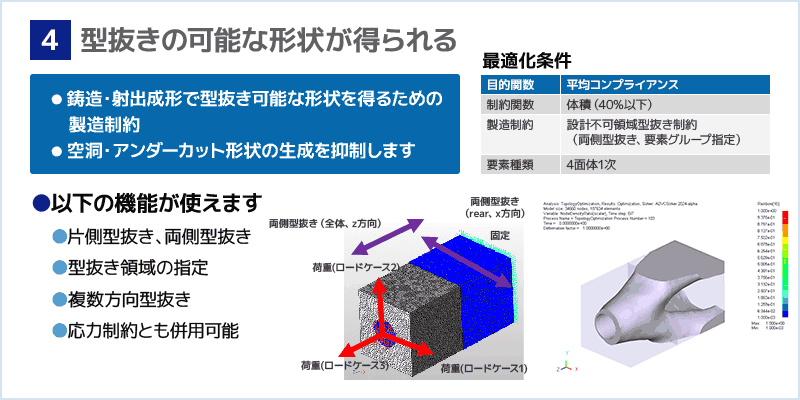
型抜き制約:事例紹介
四駆おもちゃのシャーシ形状の最適化
型抜き制約を用いた最適化事例として、電池で動く四輪駆動のおもちゃのシャーシを最適化した結果をご紹介します。 シャーシの平面図を上側に引き延ばした領域を最適化し、荷重条件としてねじり、コーナー通過時に生じる力、重量物が与える力の計5つを設定します。 形状は上下方向に離型します。
最適化の結果、型抜き制約がない場合は電池ボックスの左右に穴が開きますが、 型抜き制約を適用するとアンダーカットの発生を抑制し、電池ボックス左右の穴が埋まる結果となりました。
さらに、市販の最適化ソフトでは応力の評価と型抜き制約を同時に利用すると最適結果が得られないことが報告されていますが、 ADVENTUREClusterではこれらを同時に利用しても問題なく最適化が可能です。これもADVENTUREClusterの大きな魅力の一つです。
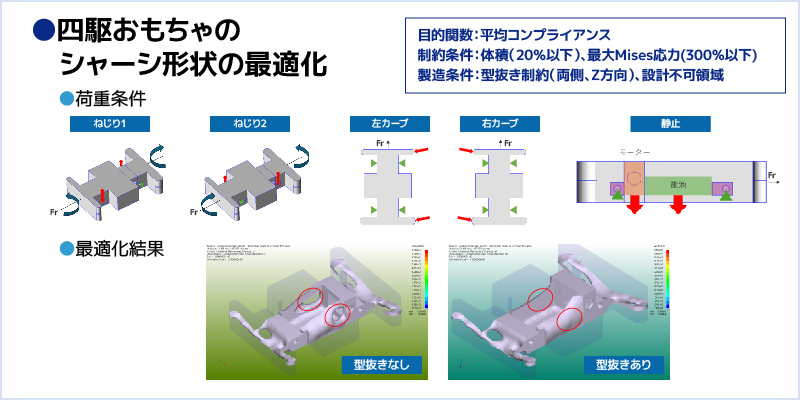
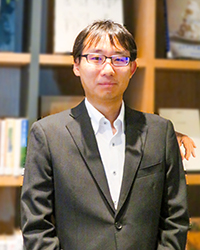
この記事を書いた人(開発者)
島田 和明 / ADVC事業部 ソルバ開発部
著者紹介
ソルバ開発部所属。2019年に入社し、主に最適化の開発に携わる。
幅広い知識と柔軟な対応力を持ち合わせ、チームの中でも頼りになる存在。
日々の業務を通じてスキルを磨き続け、新しい技術やトレンドに敏感で、常に学び続ける姿勢を持つ。
メーカー出身のキャリアを生かし、ソルバ開発に尽力している。